MULTIPORTING
Codeline pressure vessels have an advance side-porting technology. We focus on developing products that help reduce system cost.
Codeline is proud to announce multiport membrane housings with port size ranging from 1.5" up to 3" and 4".
WHAT CAN IT DO FOR YOUR SYSTEM?
Multiporting is a term used to describe membrane housing that feature more than one feed or concentrate port per end. For example, two or three ports in the feed end of a membrane housing. Multiporting allows vessels to be directly linked together. This powerful feature offers the opportunity to eliminate traditional manifolds resulting in potential system cost savings. While the cost reduction aspect of this technology is enticing, system performance must be
carefully evaluated to assure that improper port sizing does not compromise long-term system performance.
While using high flow-ported housing is not difficult, there are many variables that need to be properly addressed before vessels can be specified. To help ensure the performance of your system, please carefully consider the guidelines and pressure drop data on this page when attempting to eliminate external manifolds.
DETAILED GUIDELINES TO ELIMINATE MANIFOLDS
CAUTION: The following information are guidelines only. They are intended to aid the purchaser when using the multiport feature to eliminate manifolds. It is the system designer’s responsibility to evaluate the specific application and carefully consider these guidelines when sizing ports. Improper port sizing could lead to poor system performance and/or damage to membrane elements. Please contact Pentair if clarification of these guidelines is required.
Evaluate the pressure drop
This needs to be done across each vessel plenum as this will affect the permeate and concentrate flows in each vessel.
Typically, the feed and concentrate manifolds connecting to a number of vessels are designed to minimize variations in flow through the vessels. This is accomplished by assuring that the pressure throughout a manifold is nearly equal. The greater the differential across a particular manifold, or set of manifolds, the greater the potential for variations in the average feed pressure as well as the differential pressure across the different vessels in a pass. These factors will affect the flow of the product as well as the flow through the vessels.
The same considerations apply when attempting to eliminate manifolds by linking vessels directly together using Multiport vessels. In this case, the pressure drop across the vessel plenum, as well as the entrance and exit losses through the side ports, must be considered. To simplify this process, we have provided calculated test data, which quantifies the total pressure, drop versus the flow rate for various size ports.
Flow balance the system
This can be done by taking the combined concentrate flow from the last vessel in a particular pass.
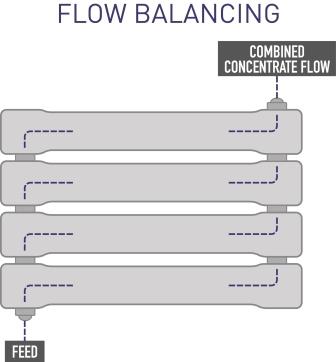
This practice is commonly used when multiple filters are connected in parallel. If the feed comes in the first vessel, the combined concentrate should exit the last vessel.
The feed pressure to the last vessel will always be less than the feed pressure to the first vessel. By flow balancing, the concentrate pressure of the last vessel will also be the lowest of any vessel. This tends to keep the pressure drop across all vessels to be as close as possible. The flow pattern is shown in Figure 1.
The down side of this arrangement is that it will cause the average feed flow pressure between the first and last vessel to be the at a maximum value, thus affecting permeate flow in the last vessel.
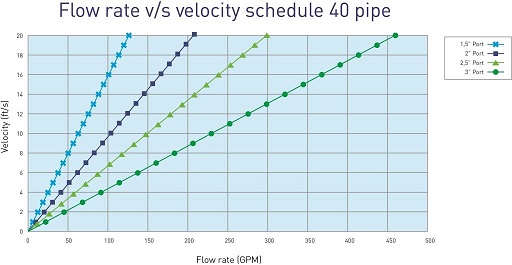
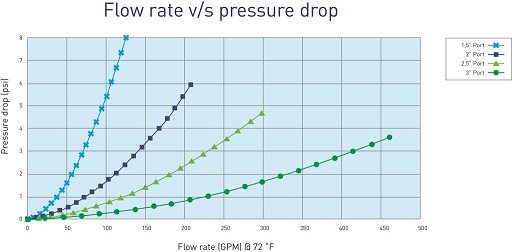
For simplicity of piping, some customers may desire to take combined concentrate flow from the first vessel in a particular pass. This will result in a lower differential pressure and thus a lower concentrate flow in the last vessel. While this practice is less conservative than flow balancing, it has been successfully used in some systems. In any event, the performance of the membranes in each vessel should be checked to confirm that all are within the membrane manufacturer’s guidelines.
Consider feeding from both sides or the center of a pass
This can be done when the differential pressure when feeding from one side would be excessive.
By splitting the feed flow the velocity will be reduced by one half and the pressure drop by an even greater amount since the pressure drop is proportional to the square of the flow. Feeding from both sides may be most economically feasible where the pressure is low enough to use plastic pipe. This option is shown in the picture below.
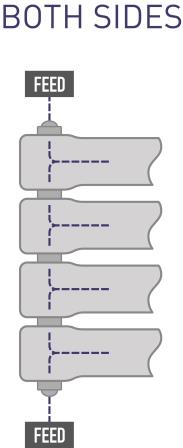
Check with your membrane supplier
The membrane supplier can help with the the evaluation of membrane performance of your proposed system.
When properly sized, use of multiport vessels to eliminate external manifolds will have little if any affect on overall system performance. However, as pressure drops are increased, systems that are already being operated close to the edge of recommended conditions may experience problems within one or more vessels. It is therefore recommended that worst case conditions be evaluated carefully in conjunction with your membrane supplier.
Consider the effects of higher velocities
These may occur during special situations such as flushing or cleaning.
It is sometimes advantageous to flush or clean systems at velocities higher than normal. These situations must be carefully considered when selecting port sizes. Pressure drops may be considerably increased under such conditions.
Pressure drops across the plenum of a vessel will always be greater than through an equal length of straight pipe of the same size as the port. For this reason you should always select ports at least equal to, and possibly greater than, the size of pipe you would use if manifolds were external
Do not reduce the size of the feed/concentrate ports
Applicable in particular pass, unless you have carefully evaluated the affect on system performance of such reductions (for brackish water desalination at the recovery above 65% the brine discharge connection size may be reduced as compared to the feed connection size).
Unlike with external manifolds, it is easy to reduce the size of ports of vessels, which are linked together. The feed port may be one size and the port directly opposite it can be specified a smaller size. This however could lead to excessive pressure drops. Again, evaluate the affects of such a design carefully.
Do not exceed traditional flow velocities
Even though the pressure drop across each vessel may be acceptable, the velocity of the water through each port must also be evaluated. It is suggested that the water velocity throughout the entire system be checked for proper velocity, however, the first connection from the feed source is typically where problems can occur. While the length of each feed port is very short, velocities in excess of 11 ft. per second should be avoided to help ensure proper system performance. We have included the published velocities for schedule 40 pipe on this page.
Do not assume, because a set of vessels can be manifolded together, that Codeline recommends or endorses such use in your particular application.Used properly, multi-porting with 3" and 4" ports opens up a whole new world of potential cost savings. With this opportunity comes a responsibility to carefully evaluate projected membrane performance. Codeline recommends that you work directly with your membrane supplier to obtain approval of your proposed design.
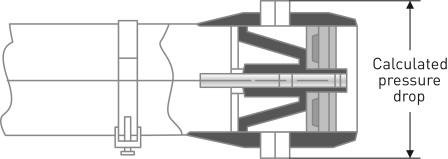
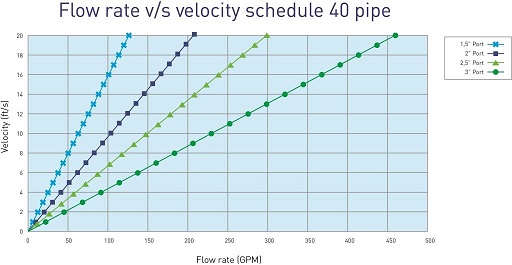
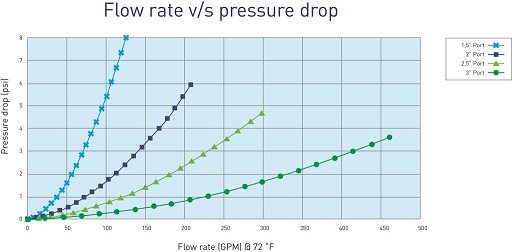